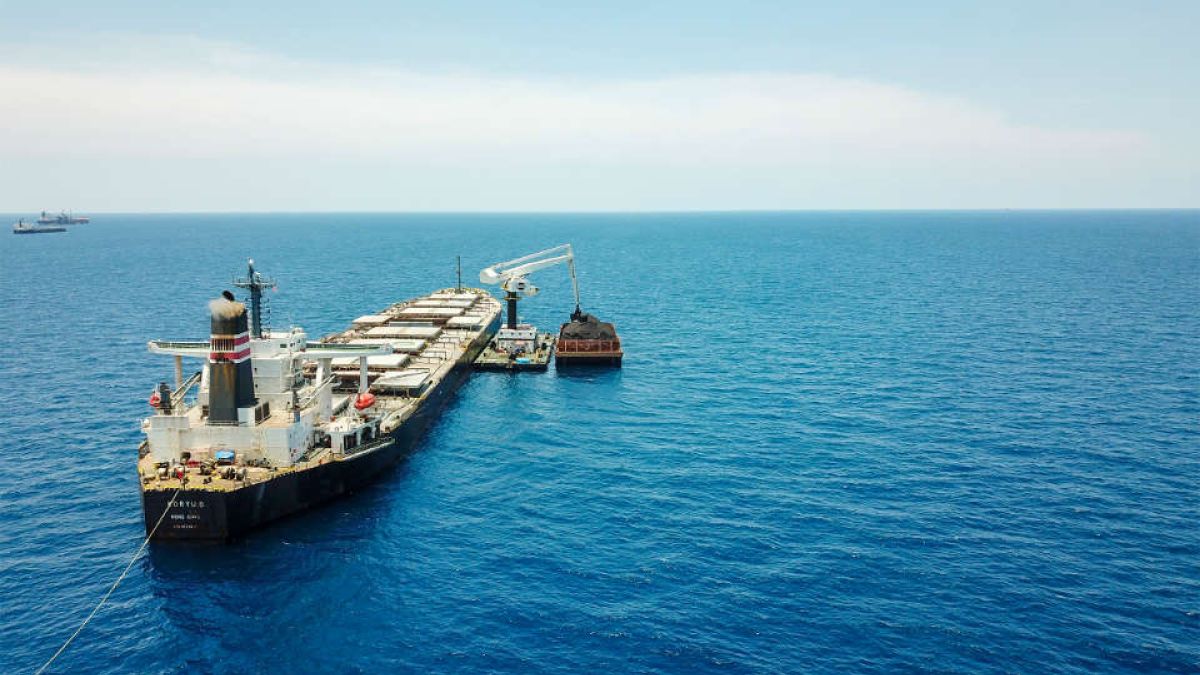
Next Generation Coal Logistics
Next generation coal logistics
Optimizing the coal supply chain is something E-Crane’s engineers and experts excel at. Solutions are offered for coal miners, (floating) terminals as well as power plants and other end users around the world. The main objective is always to provide high-end coal handling solutions built around the E-Crane, which offer a reliable and long-term operation with the lowest possible OPEX combined with the highest crane availability in the industry. This is accomplished by offering a high level of customization while, at the same, offering in depth training for operators & maintenance personnel. If users do not want to be involved in the maintenance, all-in maintenance contracts are offered so that clients can focus 100% on their core business. This is accomplished by establishing strategically placed regional service centers close to where users operate.
OPEX
E-Cranes have the lowest installed power per tonne of material handled in the crane industry. As a result of the ingenious parallelogram balance system, only a fraction of the energy is used that traditional rope cranes require to move bulk materials from point A to B. At the same time, E-Cranes are also designed according to the highest crane classification, guaranteeing a long life. These two combined guarantee an unmatched OPEX and therefore result in a good return on investment.
Training
E-Crane prides itself in not only supplying equipment, but rather long-term solutions for bulk material handling challenges. After delivery and installation, E-Crane personnel remains present on site to carry out operator and maintenance staff training, as this is a practice both client and supplier will benefit from. When it comes to in-depth training courses for operators, maintenance personnel and terminal managers, additional training can also be arranged at the E-Crane Academy at the company’s headquarters in Belgium.
(All-in) maintenance
The ultimate goal is to have 0% unscheduled stoppages throughout the life of any E-Crane. In order to get as close to this number as possible, regular site visits by a certified E-Crane field service technician are made to support the client in the best possible way and to carry out preventative maintenance tasks. E-Crane further assists in optimizing the unloading process by continued operator training, bottleneck identification and process evaluation, and by making recommendations on how the terminal operations can be optimised as a whole. With this approach a proven track record has been accomplished with crane availability being in the range of 98-99%, excluding scheduled maintenance. For this purpose, the local E-Crane service team is on standby 24/7 in case of emergencies and also guarantees the availability of replacement parts, should they be required, as part of the all-in maintenance contracts.

The human interface
At the same time there is a strong focus on creating the most ergonomic and efficient working environment for operators. This starts with a comfortable and spacious operator cab, but it is also about offering features to the crane operator that lessen operator fatigue. Examples are the semi-automatic cycle, fine control & automatic boom float, which greatly assist crane operators getting the best productivity out of the equipment, as well as help to reduce fatigue. The operator always works from an elevated position, giving him a bird’s eye view of the operation. If additional support is required, a high-quality camera system can be installed to help the operator work efficiently in even the most difficult spots, such as underneath the hatch coaming when unloading ocean-going vessels.
Analytical tools
For terminal management, a web-based analytical tool called E-CARE has been developed by the company’s software developers in close cooperation with the E-Crane design team. A large amount of data is collected on every E-Crane, and is processed and analyzed by the E-CARE software which was developed to further support E-Crane owners. Regular customizable (scheduled) reports created by this tool help both users and E-Crane’s after sales service team to get the best possible throughput rates, evaluate operator performance and efficiency & plan preventative maintenance tasks, just to name a few.
Noise reduction
A major issue in modern ports is the noise level. As more and more terminals are close to urban areas, there can be strict rules as to the maximum sound level for new equipment. Therefore, it is often a requirement that an extra effort is made to reduce any noises from the port cranes in the best way possible. Thanks to the electro-hydraulic powertrain working at relatively low hydraulic pressures, the E-Crane is already one of the quietest cranes on the market. However, as an option, E-Crane can install an additional sound dampening package to meet even the strictest demand.

Possible applications in the coal supply chain
Export logistics
Close to the coal mine in Central Kalimantan, Indonesia E-Crane has supplied a floating transfer station, which unloads coal from 180-250 ft barges and transfers it into 300 ft coal barges. Throughput rates of 1500 tph are easily reached with monthly throughput rates that have exceeded 500 000 t. The same solution can be offered for both lower and higher hourly rates.
In the next step of the supply chain, E-Cranes are used to unload barges into hoppers for storage and blending at a dedicated coal terminal. Typically, the E-Crane unloads the barges into a hopper after which the coal is conveyed to the stockpile for storage & blending. Afterwards the blended material is transported to a dedicated barge/shiploader.
In the final step of the export process, floating E-Cranes can be used to load coal into panamax & capesize vessels. This can be accomplished by utilizing a floating E-Crane or, alternatively a transhipper. Daily throughput rates of well over 70 000 tcan be accomplished, and tailor-made solutions can be designed and built according to client’s specifications. For this purpose, a detailed study needs to be carried out in order to align all links of the export process, a task that E-Crane engineers have performed many times over.
Import logistics
On the receiving end, E-Cranes are used in power & cement plants around the world to unload coal. The most commonly used solutions are floating transfer stations, fixed E-Cranes in combination with barge shifting winches (commonly used in power plants in North-America) or rail mounted E-Cranes. The latter are most often used when ocean-going vessels need to be unloaded. In this case, the preferred solution would have both the crane and hopper travel on the same rails in order to optimize the unloading cycle throughout the unloading process. For shipunloading, hourly capacities of close to 2000 tph can be accomplished, whereas in a barge unloading operation solutions of up to 3000 tph can be offered.

Conclusion
Where others claim to offer an alternative with low operating cost, combined with a high level of reliability, E-Crane really delivers — even more so when looking at machines that reach a life of 60 000 hours and more. Although E-Cranes are compatible with any type of hydraulic grab, E-Crane’s clamshell buckets are designed with a powerful closing force affording maximum fill and eliminating spills and carryback. The E-Crane operator’s cabs are equipped with a state-of-the-art control system for easy machine operation which builds operator confidence, reduces cycle times and maximises productivity.
All in all, the E-Crane design makes the machines ideally suitable for high- volume industrial and mission critical applications in the most demanding working conditions — something that has been proven many times on all continents.
Source: https://www.worldcoal.com/magazine/world-coal/october-2019/